1. Кызыл мештин кирпичи кулап жатат
Себеби:
(1) Айлануучу мештин териси жакшы илинбегенде.
(2) Цилиндр ысып кеткен жана деформацияланган, ал эми ички дубалы тегиз эмес.
(3) Мештин каптамалары жука эскиргенден кийин сапаттуу эмес же график боюнча алмаштырылбайт.
(4) Айлануучу мештин цилиндринин орто сызыгы түз эмес; дөңгөлөк кур жана аянтча олуттуу эскирген, ал эми боштук өтө чоң болгондо цилиндрдин радиалдык деформациясы күчөйт.
Көйгөйлөрдү чечүү ыкмасы:
(1) Топтоо иши жана кальцинациялоо иштери күчөтүлүшү мүмкүн.
(2) Атуу зонасына жакын дөңгөлөк кур менен жаздыкчанын ортосундагы боштукту катуу көзөмөлдөңүз. Ачыштык өтө чоң болгондо, төшөктү убагында алмаштыруу керек же төшөктөр менен жөнгө салуу керек. Төшөктөрдүн ортосундагы узак мөөнөттүү кыймылдан келип чыккан эскирүүнүн алдын алуу жана азайтуу үчүн дөңгөлөк боосу менен төшөктүн ортосуна майлоочу май кошуу керек.
(3) Меш иштеп жатканда токтоп калганын текшериңиз жана айлануучу мештин цилиндрин өз убагында оңдоңуз же ашыкча деформация менен алмаштырыңыз;
(4) Цилиндрдин борбордук сызыгын такай калибрлөө жана колдоочу дөңгөлөктүн абалын тууралоо;
(5) Жогорку сапаттагы меш каптамаларын тандап, инлейдин сапатын жакшыртыңыз, мештин каптамаларын колдонуу циклин катуу көзөмөлдөңүз, кирпичтин калыңдыгын убагында текшериңиз жана эскирген мештин каптамаларын убагында алмаштырыңыз.
2. Колдоочу дөңгөлөктүн вал сынган
Себептери:
(1) Колдоочу дөңгөлөк менен валдын дал келиши негизсиз. Колдоочу дөңгөлөк менен вал бошоп кетпеши үчүн, колдоочу дөңгөлөк менен валдын ортосундагы интерференция жалпысынан валдын диаметринин 0,6дан 1/1000уна чейин болот. Бирок, бул интерференция туура келүү валдын колдоочу дөңгөлөк тешигинин аягында кичирейип, стресстин концентрациясына алып келет. Бул жерде вал сынып калат деп элестетүү кыйын эмес, бул да.
(2) чарчоо сынганы. Колдоочу дөңгөлөктүн комплекстүү күчүнөн улам, эгерде тирөөч дөңгөлөк менен вал бир бүтүн катары каралса, валдын ийилүүчү чыңалуусу жана жылма чыңалуусу таяныч дөңгөлөктүн тешигинин учунун тиешелүү бөлүгүндө эң чоң болот. Бул бөлүк кезектешкен жүктөрдүн таасири астында чарчоого дуушар болот, ошондуктан сынык да колдоочу дөңгөлөк менен валдын ортосундагы бириктирүүнүн аягында пайда болушу керек.
(3) Өндүрүштүк кемчиликтер Роликтин валынын көбүнчө согулуп, иштетилиши жана болот куймалары же тегерек болот менен жылуулук менен иштетилиши керек. Кемчиликтер ортосунда пайда болуп, аныкталбай калгандан кийин, мисалы, болот куймасындагы аралашмалар, курт-кумурскалардын терисин согуу ж.б., жылуулук менен дарылоодо микро жаракалар пайда болот. Бул кемчиликтер валдын көтөрүү жөндөмдүүлүгүн гана чектебестен, стресстин концентрациясын да пайда кылат. Булак катары, жарака кеңейгенден кийин, жарака сөзсүз болот.
(4) Температуралык стресс же туура эмес күч Айлануучу мештин чоң плиткасын жылытуу жалпы ката болуп саналат. Эгерде эксплуатациялоо жана тейлөө туура эмес болсо, роликтин валында жер үстүндөгү жаракалар пайда болушу оңой. Чоң плитка ысыганда валдын температурасы өтө жогору болушу керек. Бул учурда, эгерде вал тез муздаса, валдын жай ички муздаышына байланыштуу, тез кичирейген валдын бети жаракалар аркылуу чоң кичирейүү стрессин гана чыгара алат. Бул учурда беттик жаракалар стресс концентрациясын пайда кылат. Алмаштыруучу стресстин аракетинде жарака тегерете кеңейип, белгилүү бир даражага жеткенде, ал үзүлөт. Роликтеги ашыкча күч үчүн да ушундай. Мисалы, туура эмес жөнгө салуу валга же валдын белгилүү бир бөлүгүнө ашыкча күч келтирет, бул роликтин валынын сынуусуна алып келет.
Четтетүү ыкмасы:
(1) Колдоочу дөңгөлөк жана вал кошулган аймакта ар кандай интерференциялар колдонулат. Колдоочу дөңгөлөк менен валдын ортосундагы интерференциянын көлөмү чоң болгондуктан, колдоочу дөңгөлөктүн ички тешигинин аягы ысык орнотулгандан, муздатылгандан жана чыңалгандан кийин бул жерде кичирейет жана стресс концентрациясы өтө чоң. Ошондуктан, долбоорлоо, өндүрүү жана орнотуу жараянында, колдоо дөңгөлөктүн ички тешигинин эки учундагы кийлигишүү көлөмү (болжол менен 100мм диапазону) акырындык менен моюндун пайда болушун жеңилдетүү үчүн ичинен сыртка азаят. Кыскартуу суммасы акырындык менен орто кийлигишүү суммасынын үчтөн бир жарымына чейин кыскарышы мүмкүн, ошондуктан, моюн кубулушун болтурбоо же азайтуу.
(2) кемчиликтерди жоюу үчүн комплекстүү кемчиликтерди аныктоо. Кемчиликтер валдын көтөрүү жөндөмдүүлүгүн төмөндөтөт жана стресстин концентрациясын пайда кылат, бул көбүнчө сыныктардын кырсыктарына алып келет. Зыян чоң жана олуттуу кабыл алуу керек. Колдоочу дөңгөлөктүн валынын кемчиликтерин алдын ала табуу керек. Мисалы, иштетүүдөн мурун материалды тандоо текшерилип, эч кандай көйгөйлүү материалдар тандалбашы керек; кемчиликтерди табуу, ошондой эле кайра иштетүү учурунда кемчиликтерди жоюу, валдын ички сапатын камсыз кылуу жана ошол эле учурда валдын кайра иштетүү тактыгын камсыз кылуу, жарака булактарын жана стресс концентрациясынын булактарын жок кылуу үчүн жүргүзүлүүгө тийиш.
(3) Кошумча жүктөрдү азайтуу үчүн мештин негиздүү тууралоосу. Бир нече ролик валдары роликтер аркылуу мештин бардык салмагын көтөрөт. Жүк абдан чоң. Орнотуу же тейлөө туура эмес болсо, эксцентрик жүк пайда болот. Мештин борбордук сызыгынан алыстык туура келбеген учурда, белгилүү бир ролик ашыкча күчкө дуушар болот; роликтин огу мештин борбордук сызыгына параллель болбогондо, валдын бир жагындагы күч күчөйт. Туура эмес ашыкча күч чоң подшипниктин ысып кетишине алып келет, ошондой эле валдын белгилүү бир жеринде чоң стресстен улам валга зыян келтирет. Ошондуктан, мешке тейлөө жана жөндөө кошумча жүктөрдү болтурбоо же азайтуу жана мештин жеңил иштөөсүнө олуттуу мамиле кылуу керек. Тейлөө процессинде валда отту жана ширетүүдөн качыңыз жана валдын бузулушун азайтуу үчүн валды майдалоочу дөңгөлөк менен майдалоодон алыс болуңуз.
(4) Иштеп жатканда ысык валды тез муздатпаңыз. Мештин иштөө учурунда чоң подшипник кандайдыр бир себептерден улам ысытууну пайда кылат. Бул убакта өндүрүштүк жоготууларды азайтуу үчүн, кээ бир агрегаттар тез муздатууларды кабыл алышат, бул валдын бетинде микро жаракаларды пайда кылуу оңой, ошондуктан тез муздабаш үчүн жай муздатуу кабыл алынышы керек.
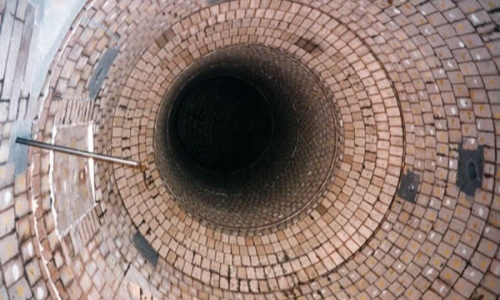
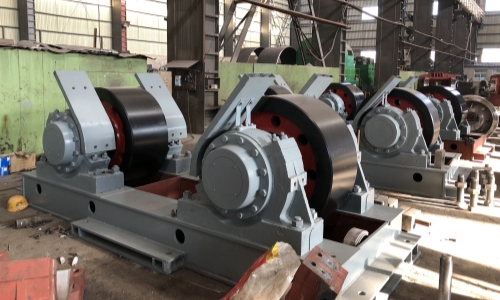
Посттун убактысы: Май-12-2025