Төмөн цементтин отко чыдамдуу куюлган материалдары салттуу алюминат цементинин отко чыдамдуу куюлган материалдарына салыштырылат.Салттуу алюминат цемент отко чыдамдуу куюлган цементтин кошулмасынын өлчөмү, адатта, 12-20%, ал эми суу кошуунун көлөмү жалпысынан 9-13% түзөт.Кошулган суу көп болгондуктан, куюлган дененин тешикчелери көп, тыгыз эмес, күчү аз;көп сандагы цемент кошулгандыктан, жогорку нормалдуу жана төмөнкү температуралык бекемдиктерди алууга мүмкүн болсо да, орточо температурада кальций алюминатынын кристаллдык өзгөрүшүнө байланыштуу бекемдик төмөндөйт.Көрүнүп тургандай, киргизилген СаО SiO2 жана Al2O3 менен куюлуучу зат менен реакцияга кирип, эрүү температурасы төмөн болгон кээ бир заттарды пайда кылат, натыйжада материалдын жогорку температуралык касиеттери начарлайт.
Ультра майда порошок технологиясы, жогорку эффективдүү аралашмалар жана илимий бөлүкчөлөрдүн градациясы колдонулганда, куюлган цементтин курамы 8% дан азыраак жана суунун мазмуну ≤7% га чейин азаят жана аз цементтүү сериядагы отко чыдамдуу куюлган болот. даярдалган жана киргизилген СаО мазмуну ≤2,5% түзөт жана анын иштөө көрсөткүчтөрү көбүнчө алюминат цементинин отко чыдамдуу куюлуучу материалдарынан ашып кетет.Отко чыдамдуу куюлмалардын бул түрү жакшы тиксотропияга ээ, башкача айтканда, аралаш материал белгилүү бир формага ээ жана бир аз тышкы күч менен агып баштайт.Тышкы күч алынып салынганда, ал алынган форманы сактап калат.Ошондуктан, ал тиксотроптук отко чыдамдуу куюлуучу деп да аталат.Өзүн-өзү аккан отко чыдамдуу куюлуучу, ошондой эле тиксотроптук отко чыдамдуу куюлуучу деп аталат.Бул категорияга кирет.Төмөн цемент сериясы отко чыдамдуу куюлуучу материалдардын так мааниси ушул кезге чейин аныктала элек.Американын Сыноо жана Материалдар Коому (ASTM) алардын CaO мазмунунун негизинде отко чыдамдуу куюлмаларды аныктайт жана классификациялайт.
Жыш жана жогорку күч - аз цементтүү сериядагы отко чыдамдуу куюлуучу конструкциялардын өзгөчөлүгү.Бул продуктунун кызмат мөөнөтүн жана өндүрүмдүүлүгүн жакшыртуу үчүн жакшы, бирок аны колдонуудан мурун бышыруу кыйынчылыкка алып келет, башкача айтканда, бышыруу учурунда этият болбосоңуз, куюу оңой болуп калышы мүмкүн.Дененин жарылуу көрүнүшү жок дегенде кайра куюуну талап кылышы мүмкүн, же оор учурларда курчап турган жумушчулардын жеке коопсуздугуна коркунуч келтириши мүмкүн.Ошондуктан, ар кандай өлкөлөр, ошондой эле аз цемент сериясы отко чыдамдуу куюлган бышыруу боюнча ар кандай изилдөөлөрдү жүргүзгөн.Негизги техникалык чаралар: мештин ийри сызыктарын калыптандыруу жана жарылууга каршы эң сонун каражаттарды киргизүү жана башкалар. Бул отко чыдамдуу куюлмаларды жасай алат. Суу башка терс таасирлерди пайда кылбастан бир калыпта жок кылынат.
Ультра майда порошок технологиясы аз цементтүү сериядагы отко чыдамдуу куюлмалардын негизги технологиясы болуп саналат (учурда керамика жана отко чыдамдуу материалдарда колдонулган ультра жука порошоктардын көпчүлүгү чындыгында 0,1 жана 10 м ортосунда жана алар негизинен дисперсиялык тездеткичтер жана структуралык тыгыздаткычтар катары иштешет. .Биринчиси цемент бөлүкчөлөрү флокуляциясыз жогорку дисперстүү, ал эми акыркысы куюучу корпустагы микротешикчелерди толук толтурат жана бекемдигин жакшыртат.
Учурда кеңири колдонулган өтө майда порошок түрлөрүнө SiO2, α-Al2O3, Cr2O3 ж.б. кирет. SiO2 микропорошокунун өзгөчө аянты болжол менен 20м2/г, ал эми анын бөлүкчөлөрүнүн өлчөмү цементтин бөлүкчөлөрүнүн өлчөмүнүн 1/100 бөлүгүн түзөт, ошондуктан ал жакшы толтуруу касиеттери.Мындан тышкары, SiO2, Al2O3, Cr2O3 микропорошок жана башкалар сууда коллоиддик бөлүкчөлөрдү пайда кыла алат.Дисперсант болгондо, бөлүкчөлөрдүн бетинде бири-бирин кайталаган электрдик кош катмар пайда болуп, электростатикалык түртүүнү пайда кылат, ал бөлүкчөлөрдүн ортосундагы ван-дер-Ваальс күчүн жеңип, интерфейс энергиясын азайтат.Ал бөлүкчөлөрдүн ортосундагы адсорбцияны жана флокуляцияны алдын алат;ошол эле учурда дисперсант бөлүкчөлөрдүн айланасына адсорбцияланып, эриткич катмарды пайда кылат, бул да куюлуучу заттын суюктугун жогорулатат.Бул ошондой эле өтө майда порошок механизмдеринин бири болуп саналат, башкача айтканда, ультрафиолет порошок жана тиешелүү дисперсенттерди кошуу отко чыдамдуу куюлмалардын суунун чыгымын азайтып, суюктукту жакшыртат.
Төмөн цементтүү отко чыдамдуу куюлуучу материалдарды орнотуу жана катуулатуу гидраттык байланыштын жана когезиялык байланыштын биргелешкен аракетинин натыйжасы болуп саналат.Кальций алюминат цементинин гидратация жана каттуулугу негизинен CA жана CA2 гидравликалык фазаларынын гидратациясы жана алардын гидраттарынын кристаллдык өсүү процесси, башкача айтканда, алар алты бурчтуу кабыкча же ийне сымал CAH10, C2AH8 жана гидрациялык продуктуларды пайда кылуу үчүн суу менен реакцияга кирет. куб C3AH6 кристаллдары жана Al2O3аq гелдери катары, андан кийин айыктыруу жана ысытуу процесстеринде өз ара байланышкан конденсация-кристаллдашуу тармагынын структурасын түзөт.Агломерация жана байланыш активдүү SiO2 ультра майда порошок сууга жолугуп, коллоиддик бөлүкчөлөрдү түзүүчү жана кошулган кошумчадан (б.а. электролит заты) акырындык менен диссоциацияланган иондорго жолугуусу менен шартталган.Экөөнүн беттик заряддары карама-каршы болгондуктан, башкача айтканда, коллоиддик бет карама-каршы иондорду адсорбциялагандыктан, £2 пайда кылат.Башкача айтканда, коллоиддик бөлүкчөлөрдүн бетиндеги электростатикалык түртүү анын тартылуусунан аз болгондо, ван-дер-Ваальс күчүнүн жардамы менен когезиялык байланыш пайда болот.Кремний диоксиди порошок менен аралаштырылган отко чыдамдуу куюлуучу зат конденсациялангандан кийин, SiO2 бетинде пайда болгон Si-OH топтору кургатылат жана көпүрөгө чейин суусуздандырылып, силоксан (Si-O-Si) тармак структурасын түзүшөт, ошону менен катуулашат.Силоксан тармагынын түзүлүшүндө кремний менен кычкылтектин ортосундагы байланыштар температуранын жогорулашына жараша азайбайт, ошондуктан күч дагы жогорулайт.Ошол эле учурда, жогорку температурада, SiO2 тармагынын түзүмү ага оролгон Al2O3 менен реакцияга кирип, муллит пайда кылат, бул орто жана жогорку температурада күчтү жакшыртат.
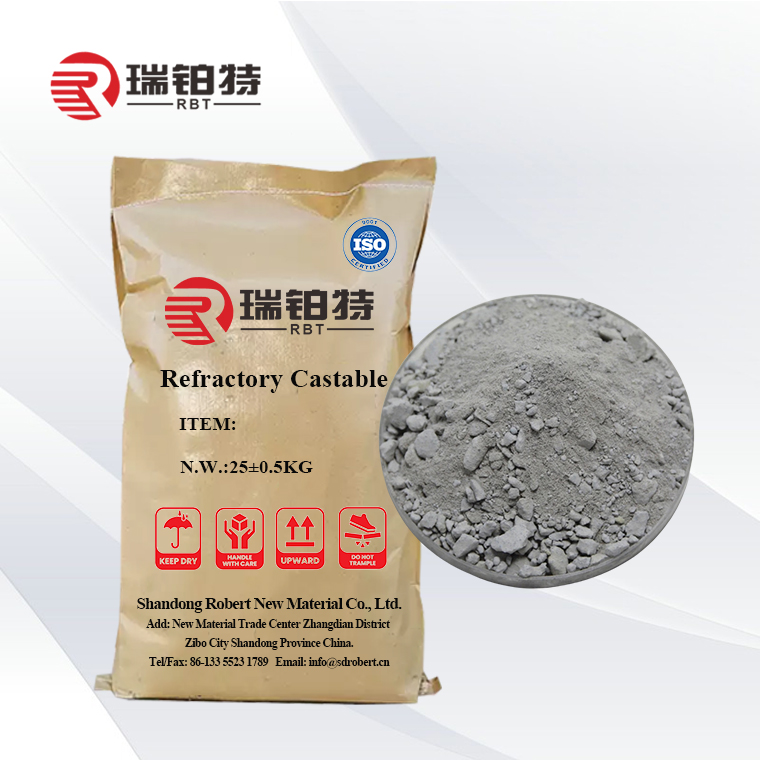
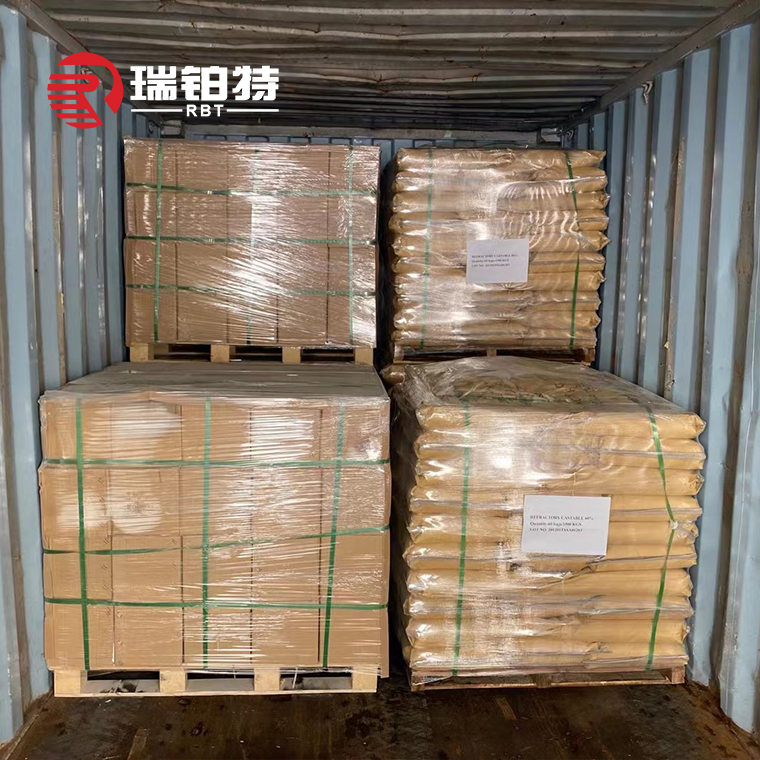
Посттун убактысы: 28-февраль 2024-ж